Powder Metallurgy

What is Carbonyl?
As it is known, there are two common systems for separating metals from their natural state; Hydrometallurgy and Pyrometallurgy. In one, metals are separated from the rock with the help of water and chemicals, while in the other, heat is generally used. Carbonyl, as a third alternative, was discovered by scientists in the late 1800s and continues to develop until today, although not very rapidly.
Although there are many methods for producing metal powders, Carbonil is at the top level of this sector because it is a refinery system and powder can be produced with the smallest size and spherical shape.
Only a few large companies in the world have developed the technology with their R&D groups and produce metal powder by establishing their own facilities. For example, the first iron carbonyl plant was established in Germany in 1925. The Nickel facility in Russia has been producing Nickel Powder for more than 30 years. However, there are very few laboratories available to conduct experiments within the scope of this technology.
In general, carbonyl is based on the principle of providing certain thermodynamic conditions on the ore and feeding carbon gases into the reactor to form compounds in this process. In this process, metals are separated from the ore zone on an atomic basis, transform into another form and are decomposed in the environment. Afterwards, the conditions are changed to obtain pure metal powder from this intermediate compound in micron and sometimes even submicron sizes. This means that it becomes a perfect raw material for industrial processing.
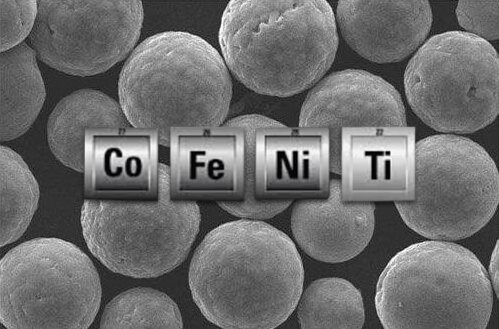
Where is Powder Metal Formed with Carbonyl Used?
The global Powder Metallurgy market size reached 2.58 Billion USD in 2022. Looking forward, it expects the market to exhibit a CAGR of 9.80% during 2023-2027, reaching a value of $4.63 Billion by 2027.
The most important areas of use of metal powders are MIM (Metal Injection Molding) and DMLS (Direct Metal Laser Sintering) methods. In MIM, the product is obtained by pressing the powder into a mold with a by-product, while in DMLS management, high quality parts are produced using 3D printers.
In the compound prepared by melting and pouring into the crucible in classical methods, the material strength remains at the same level due to hairline cracks and air voids that form upon cooling. However, when MIM and DMLS technologies are used, high-strength products can be easily achieved since very small-sized pure metals are connected with an atomic bond without any gaps. As can be seen in the photo below, unlike classical methods, it can produce high-level tension-resistant materials with almost no voids (>97% density).
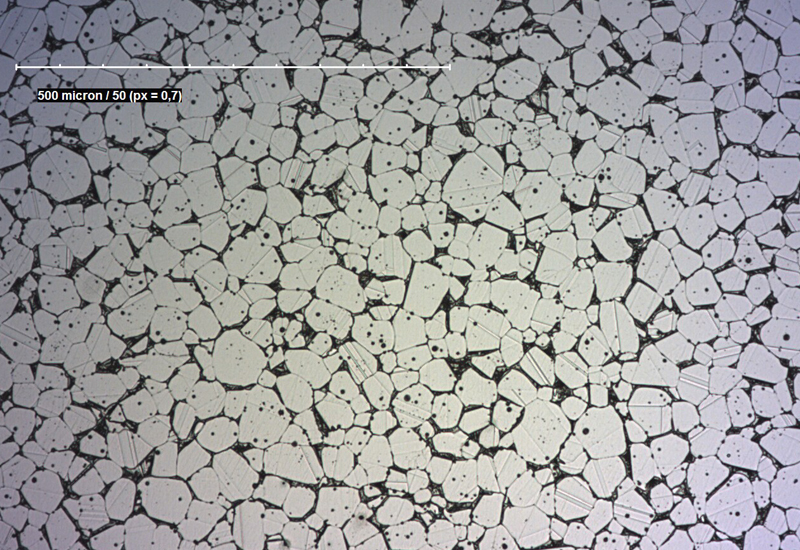
Especially the companies that make MIM and DMLS in the world are Defense Industry (rocket, aircraft parts, weapon parts), Medicine (Medical equipment parts), Aerospace parts, Automotive and all general industry companies.
The use of powder metal is also increasing in battery technologies. Many companies are experimenting with the use of powdered metal for fast charging and long battery life and are currently using these products.
For example, this photo shows a Rocket Engine Part produced from powder metals with a 3D printer. These micron-sized metal powders are incredibly useful for materials that are smaller than 200 grams and very durable, and the technology is gradually developing.

Apart from these, other uses of powder metals are:
• Powder Metallurgy (PM)
• Fiber Production – Hot Polymer Filtration
• Surface coating / Hard coating
• Metal Injection Molding
• Pharmaceutical Industry
• Paint Additives
• Food Equipment
• Pressure Vessels Production
• Structural Transition Joints
In Which Mines Can Carbonyl Technology Be Used?
Companies that have been producing metal powder in this system for many years primarily produce Iron, Nickel and Cobalt powder. However, there are over thirty minerals that have been tested for suitability to the system and are suitable for the use of Carbonyl technology. Rare earth elements are also important recoverable metals of this group. Carbonyl, a very specific system, acts as a refinery and can purify even minerals that are very difficult to capture at atomic scale.
Is Carbonyl a Harmful Method?
In this method, which does not use any liquids or chemicals, reactions take place only with certain gases, pressure and temperature balances. Since all gases used in the system are recovered and reused, the entire cycle remains within the system. The release of these gases into the environment is prevented in the facility within the scope of the “0 Emission” philosophy, creating zero waste for the environment. Since there is no carbon emission and no liquid usage, this technology does not contain parts such as tailings dams that could potentially threaten the environment.
The system, which provides great advantages especially in EIA, has the potential to create an alternative for many problematic projects.